Automotive wiring harness is an important part of automotive electrical and electronic systems, but also the vehicle fault multiple links. How to improve the reliability of the work of the wiring harness in the design process, reduce the vehicle failure rate, ensure the failure in the shortest time to eliminate the fault, become the focus of automotive electrical system design. In this paper, the design principle of vehicle electrical harness layout is analyzed and discussed systematically.
Automotive electrical system design from the vehicle or assembly project started, the main design process shown in Figure 1. As the key stage of the design process, the electrical system design and electrical system three-dimensional layout need to be synchronized, if the electrical system design is compared to the soul, then the three-dimensional layout of the electrical system is carrying the soul of the body. The quality of the three-dimensional arrangement of the electrical system directly affects the quality of the prototype of the prototype, and the efficient three-dimensional arrangement can reduce the problems in the trial production process, reduce the trial cost and shorten the vehicle design time.
The three-dimensional arrangement of the electrical system mainly refers to the use of CATIA, PRONE and other three-dimensional software on the vehicle electrical components, wiring harness and related fixed structure in the vehicle layout, including three-dimensional layout of electrical components and electrical wiring three-dimensional layout of two parts, According to the specific structure of the vehicle layout. This paper summarizes some basic principles and precautions based on the experience of the three-dimensional layout of the actual automotive wiring harness, which mainly elaborates from the harness assembly, the harness maintenance and the harness safety and so on, and provides the basic design for the three-dimensional layout design of the automobile electrical wiring harness Guidelines.
1, the general process of three-dimensional layout of automotive wiring harness
The three-dimensional layout of the automotive electrical system is carried out according to the design flow shown in Fig. The electrical system of the vehicle is divided into different modules such as chassis, dashboard, engine and transmission according to the location. The electrical equipment is arranged for each module. The work is done by the electrical system designer and the vehicle system engineer. After the electrical equipment layout is determined, the wiring harness will be designed and the wiring harness will be designed according to the principle of the layout of the electrical wiring harness, and the scheme will be verified until reasonable. After the electrical harness is designed, the fixed mode and structure are determined according to the wiring harness, and the strength and interference check of the fixed mode and structure are carried out. The two-dimensional map of the electrical harness and the fixed structure are drawn according to the final design scheme. The following mainly discusses the basic design principles and precautions in the process of automobile wiring harness.
2, the basic principles of wiring harness layout and precautions
In the three-dimensional design of the automotive wiring harness, we must fully combine the body of rice, frame and other harness attachment of the specific circumstances of the vehicle electrical comprehensive comprehensive consideration. The wiring harness layout design should also take into account the wiring harness fixation problem, according to the structure of rice fittings, vehicle mechanical structure to determine the fixed mode and the number of fixed points; controller and need to focus on the layout of the case, the controller layout To be considered.
2.1, easy to install
In the automotive wiring harness layout of the main focus on two aspects: the wiring harness itself easy to install; wiring harness fixed structure easy to assemble.
2.1.1, the wiring harness assembly is easy to assemble
Automotive wiring harness layout should be considered as far as possible not to the vehicle assembly process to add too much process, for different parts of the vehicle can be used to sub-packaging, such as dashboard, doors, roof, left and right body. And in the design process to consider the characteristics of different regions, the design of the wiring harness must not affect the other parts of the vehicle assembly; in the wiring harness hole, the required hole of the outer envelope of the largest diameter of the connector , Its diameter must be less than the diameter of rice hole, otherwise it will cause the harness can not pass through.
2.1.2, harness fixed structure easy to install
In the design of wiring harness fixed and fixed structure must consider the assembly, not in the pursuit of fixed and reliable at the same time to the assembly process to add too many processes, according to the actual design experience summed up the following precautions.
1), as far as possible the use of simple fixed way, especially for small space areas, such as the door line, white body and interiors between the line, because of its small space, try to use plastic buckle or tape fixed.
2), through-hole rubber sheath should be designed to less than 100 N in the case of installation, you can fully assembled in the rice gold hole.
3), for the need to use your fingers to press the fixed parts, the operating force of 45 N; hand press the fixed parts, the operating force of 75 N.
4), in the wiring harness fixed structure and related functional box design process, as far as possible the use of commonly used standard parts, and standard parts as little as possible, through the early design to reduce the assembly and maintenance of special tools used.
5), for the assembly of the connector or wiring harness fixed structure through the cab situation, the fasteners if the use of ordinary hex nuts and bolts, a person is difficult to complete independently, this time generally consider the use of welding nuts or self-attack Nails are fixed.
6), the harness of the fixed hole to open as far as possible in the plane of the structural parts, fixed on the surface, it is best to make a small plane on the structure.
7), in the electrical wiring layout, as far as possible to consider the large assembly modular assembly, improve the production line assembly speed. Such as transmission harnesses, engine harnesses are fitted to the transmission and engine body, respectively, and then assembled as a unit to the chassis.
2.2, good maintainability
In the vehicle electrical wiring harness layout, we should pay attention to after-sales maintenance links. Good maintainability is reflected in the event of an electrical system failure, troubleshooting in the shortest possible time, and troubleshooting to avoid damage to other components during troubleshooting. If the wiring harness or electrical parts of the problem, the demolition should be simple, while the demolition does not affect other unrelated parts, otherwise it will cause some unnecessary waste, increase maintenance time. Therefore, to ensure that the vehicle electrical system has a good maintainability, electrical wiring harness layout to take into account the following aspects.
1), the harness connector is arranged as far as possible within reach.
2), harness connector if only one hand plug, the plug to be firmly fixed.
3), the same part of the connector to use color, size, internal positioning and other methods to distinguish, to prevent the wrong plug.
4), the end of the wiring harness should be reserved for a certain length, in order to facilitate the plug plug: for the switch end of the wiring harness recommended to reserve 80 ~ 100 mm, combined instrument, audio, air conditioning panel, fuse box and other maintenance The higher the electrical parts, the rear harness according to the assembly installation location reserved for easy to plug the length. Figure 3 for a off-road vehicle dashboard function switch wiring harness, in order to facilitate the function switch disassembly, maintenance, in the wiring harness design here, the function switch branch reserved for 100 mm margin.
2.3, the wiring harness has good reliability
How the wiring harness is reliable is also the problem that needs to be considered when the automobile electrical wiring harness is arranged. It mainly protects the harness body by adopting the harness cover, protects the harness through the gold hole, increases the harness fixing bracket, Under the wiring harness and other measures to reduce the wiring harness to improve the reliability of a job.
1), the harness through the rice hole, through the increase through the hole sheath to avoid the metal parts of the harness wear.
2), the harness across the rice when the gold, in order to avoid the edge of the rice grain on the harness caused by wear and tear, consider the use of special-shaped cable or rice pieces on the increase in rubber pieces to do protection.
3), the harness should be arranged along the edge, along the slot, to prevent the harness directly under pressure.
4), the size of the wiring harness should be in accordance with the provisions of QC / T 29106, where the basic dimensions of the wiring harness limit value as shown in Table 1.
5), the wiring harness diameter is too large need to bend a certain angle to set aside enough space, the general wiring harness bending radius is greater than twice the diameter of the harness, the problem in the head connector to focus on the root to avoid bending space Small damage to harness and connector.
6), all arranged in the vicinity of the movement of the wiring harness, and moving between the pieces should be at least 50 mm gap.
7), the two pairs of moving parts on the wiring harness, must be fixed to each moving parts.
8), the moving parts, the opening and closing parts (such as the door), between the wiring harness to retain the maximum opening length, and consider the minimum opening of the parts when the accumulation of space and fixed mode. Figure 4 shows a light vehicle door and white body wiring harness transition, in the wiring harness design to consider the maximum opening of the door, and according to the maximum opening of the door when the distance between the door and the white body to determine the length of the harness After the length of the need to verify the door closed when the door and white body gap size, in order to avoid closing the door to the harness jacket and harness caused by extrusion, in the door or white body corresponding to the location of the area to do concave processing.
9), the distance between adjacent fixed points of a long beam can not be greater than 300 mm, and the maximum distance between adjacent fixed points can not exceed 400 mm when the body structure can not be guaranteed.
10), the wiring harness bending, bending points should be set before and after the fixed point.
11), rice alloy structure is not allowed to open the hole, you can consider the welding rod or welding convex bracket and convex bolt (column), the wiring harness fixed.
12), the need to connect outside the electrical parts of the connector and need to re-plug back to the fixed wiring harness, in order to ensure the maintenance of the harness and leaving the length required to pull out the operation, but also consider the fixed wiring harness stacking space and wiring harness fixed the way.
13), the design wiring harness must have sufficient slack (greater than the minimum length of the harness 25 mm), so that it does not produce prestressed device connected.
14), due to vehicle differentiation, the assembly is not used when the wiring harness branch, in accordance with 100 ~ 200 mm straight out as shown in Figure 5 fixed on the main line or bracket, bundled wiring harness minimum bending radius can not be less than the diameter of the harness 2 times. For example, the off-road truck harness is equipped with the tire lift switch branch, because the car spare tire lift switch is arranged in the car, so in the chassis assembly need to bundle the bundle tightly tied to the chassis harness trunk.
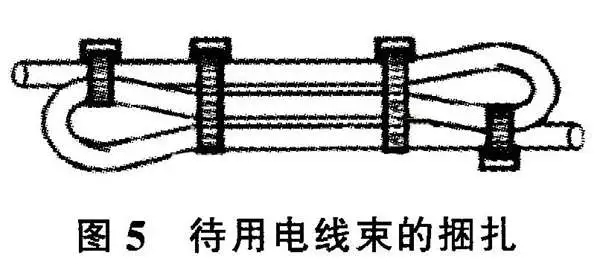
15), according to the different position of the harness, different working conditions, the design of different harness protection forms, such as door harness and interior trim inside and outside the body wiring harness, due to space is small, generally consider the use of tape protection; chassis and body contact more, And exposed to the outside, generally with a waterproof performance of the closed bellows protection; in the vehicle temperature higher parts (such as engines, etc.), near the wiring, need to take insulation measures.
2.4, the electrical circuit as short as possible
The electrical harness circuit must be as short as possible. Consider a good demolition process, we must consider how to minimize the wire loop, because the shorter loop has the following advantages:
① line segment consumption voltage is low, the voltage can be matched to the electrical device, their corresponding signal strength is high;
② reduce vehicle quality;
③ reduce the cost of wiring harness.
2.5, harness segment design should be careful
Sometimes in order to achieve the assembly of the craft, in the automotive electrical wiring harness three-dimensional design may be the original paragraph can be divided into two sections of the wiring harness, it is bound to increase the harness connector, in the sub-design for plug The following are some questions to consider.
1), the total voltage drop across the wire harness increases, and the signal strength on the electrical device is attenuated.
2), the increase in the connector, is bound to cause an unreliable connection of electrical connections increased.
3), in order to fix the increase in the connector, it is bound to increase the bracket or consider other fixed way.
4), increase the wiring harness assembly time and material costs.
In view of the above, in the circumstances permitting, as far as possible to reduce the wiring harness, through the use of through the wiring harness design.
3, summary
With the development of vehicle electrical and electronic technology, more and more vehicle equipment, and thus the reliability of the vehicle electrical wiring harness more and more demanding. Reasonable and reliable electrical wiring harnessing in the electrical system development phase can shorten the development cycle, reduce vehicle costs and improve the reliability of the electrical system. How to use three-dimensional software on the electrical three-dimensional layout of a more accurate design requires us to continue to explore.